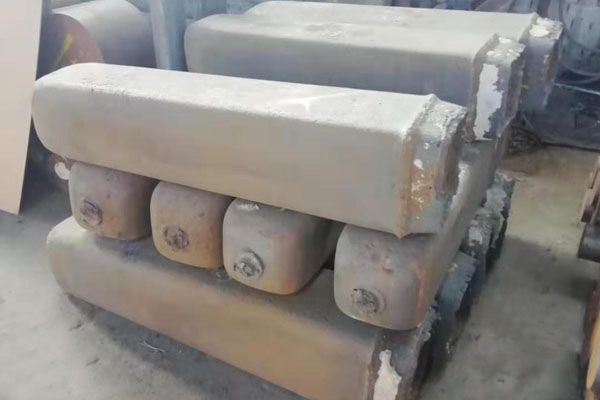
钢水经盛钢包注入铸模凝固形成钢锭。钢液在炼钢炉中冶炼完成后,必须铸成一定形状的锭或坯才能进行加工。用铸模铸成钢锭的工艺过程简称为铸锭。
钢锭至今仍是轧钢生产的主要原料。钢锭质量的优劣、锭型的状况以及其重量大小对轧钢生产有着十分重要的作用。在轧钢生产中除各类初轧机可选用钢锭作原料外,一些特殊用途轧机、部分中厚板轧机也用钢锭为原料,我国不少地方中小企业的开坯机成品轧机也选用小钢锭作原料。钢锭选择的内容主要是正确地选择钢锭种类、它的重量以及断面形状和尺寸大小。
钢锭一般情况下大致可区分为以下几类:
未净钢
钢锭只经过了基本(低限)的脱氧处理。钢锭凝固时,钢锭模的四周及底部生成一层接近纯铁的金属层,而碳、硫及磷等则于中央收缩孔附近生成偏折。金属中的氧,会生成一氧化碳卷在金属内生成气孔,但气孔会在热轧过程中消失。未净钢的优点在于可获得几无缺陷的钢材表面---表面几为纯铁的缘故。绝大部份的未净钢含碳量均为小于0.1%的低碳钢。
盖帽钢(加盖钢)
液中的氧使钢锭的收缩中心附近的偏折情形,较未净钢为低,表面美观,内部化学成份均匀,机械性质也较未净钢为佳。
全净钢
液中的氧早在凝固前便完全被脱除成限制在低限以内避免未净钢的边缘效应。脱氧处理,由在钢液中添加铁—硅合金使钢液中的氧反产生成熔渣而得到均匀的金属液。
半净钢
半净钢介于未净钢与全净钢之间,钢液中经加了少量的铁——硅或铝做为除氧剂,添加的量正好足够去除未净钢的边缘效应,使氧获得充份的分解。
真空除氧钢(真空除气钢)
藉由真空处理不需添加任何除氧元素,使钢液得到充份的除氧效果且钢中不生成非金属介在物。处理过程是先增加钢中的碳含量,然后将钢液经真空浇铸,此时碳与氧将反应生成一氧化碳而使钢液中的碳与氧逐渐降至规定的水准。由于过程中未添加会生成固态氧化物的除氧元素,钢质非常干净。
钢锭
除此之外,因浇铸前钢液中含氧量的不同,钢锭分为镇静钢、沸腾钢和半镇静钢三种基本类型。
镇静钢
又称全脱氧钢,是凝固过程中钢液内氧含量低到不会与钢中碳反应生成一氧化碳气泡的钢。铸前钢液须经充分脱氧,如用硅和铝脱氧,钢中硅含量在0.3%左右,铝含量在(0.02~0.06%)。镇静钢锭均有缩孔,必须用带保温帽的锭模浇铸。轧制后经过切头,钢锭成坯率为85~89%。要求成分均匀、组织致密的钢材采用这种钢锭。镇静钢采用上大下小带保温帽的铸模。近年广泛采用发热保温帽和隔热板保温帽等以提高成坯率。
沸腾钢
钢液中含氧量较高(0.02~0.04%)、在锭模中发生强烈碳氧反应、生成一氧化碳气泡,使钢液在模中沸腾而得名。这种钢凝固一开始,气泡就形成并上浮。钢锭表皮凝固成含铁较纯的壳层。当表层达到所要求的厚度时,在钢锭顶部加上盖板,使顶部凝固,阻止气泡继续逸出;也可在顶部加入硅铁、铝等脱氧进行化学封顶;也有用瓶口式锭模进行封顶。另一种方法是在钢液凝固成表面层后即向整体钢液中加铝脱氧,这种钢锭称为外沸内镇钢。沸腾钢一般采用上小下大敞开式的瓶口式铸模。沸腾钢锭成坯率高达90~92%,主要用于低碳钢。
半镇静钢
介于镇静钢和沸腾钢之间的钢种。这种钢内部气体少,结构接近于镇静钢。半镇静钢浇铸初期不产生气泡,当顶部自然凝固封顶后(可采用瓶口模促进封顶),由于钢液中碳和氧的富集和温度降低,促使在钢锭顶部产生少量一氧化碳气泡,填充整个钢液的凝固收缩空间。因此,可得到与沸腾钢相近的钢锭成坯率。半镇静钢主要用于中等碳含量和中等质量的结构钢,所用铸模一般为敞开式上小下大型。
脱模 浇铸完毕的钢锭,需待内部完全凝固后方可脱模。对裂纹敏感性强的合金钢锭,脱模后应在热状态(>900℃)放入缓冷坑中保温缓冷,或在不低于750℃温度下热送入轧钢车间的均热炉或加热炉。
锻圆厂家定制哪家好,就找唐山盛通锻造有限公司。
The molten steel is injected into the mold through the ladle and solidified to form a steel ingot. After the molten steel is smelted in the steelmaking furnace, it must be cast into a certain shape of the ingot or billet for processing. The process of casting a steel ingot by a mold is simply referred to as an ingot.
Steel ingots are still the main raw material for rolling steel production. The quality of the ingot, the condition of the ingot type and its weight play a very important role in rolling steel production. In the steel rolling production, in addition to various types of roughing mills, steel ingots can be used as raw materials. Some special-purpose rolling mills and some medium-thick plate mills also use steel ingots as raw materials. In many local small and medium-sized enterprises, the mills for rolling mills also use small steel ingots as raw materials. . The selection of ingots is mainly to correctly select the type of ingot, its weight, and the shape and size of the section.
Steel ingots can generally be divided into the following categories:
Unclean steel
The ingots have only undergone the most basic (lower limit) deoxidation treatment. When the ingot is solidified, a layer of metal close to pure iron is formed around the bottom and bottom of the ingot mold, and carbon, sulfur and phosphorus are deflected near the central shrinkage hole. Oxygen in the metal creates a carbon monoxide roll that creates pores in the metal, but the pores disappear during the hot rolling process. The advantage of uncleaned steel is that it can obtain several flawless steel surfaces - the surface is pure iron. Most of the unpurified steel has a carbon content of less than 0.1%.
Cap steel (capped steel)
The oxygen in the liquid causes the deflection of the steel ingot near the center of shrinkage to be lower than that of the unpurified steel, the surface is beautiful, the internal chemical composition is uniform, and the mechanical properties are better than those of the unpurified steel.
Full net steel
The oxygen in the liquid is completely removed before it is solidified to be limited to the lower limit to avoid the edge effect of unclean steel. In the deoxidation treatment, an iron-silicon alloy is added to the molten steel to cause oxygen in the molten steel to be reversely generated into slag to obtain a uniform molten metal.
Semi-clean steel
Semi-clean steel is between unpurified steel and all-purified steel. A small amount of iron-silicon or aluminum is added as an oxygen scavenger in the molten steel. The amount added is just enough to remove the edge effect of unpurified steel and make oxygen. Get a full breakdown.
Vacuum deoxidized steel (vacuum degassing steel)
By vacuum treatment, it is not necessary to add any oxygen scavenging element, so that the molten steel can obtain a sufficient oxygen scavenging effect and no non-metal intervening material is formed in the steel. The treatment process is to first increase the carbon content in the steel, and then the molten steel is vacuum casted, at which time carbon and oxygen will react to form carbon monoxide to gradually reduce the carbon and oxygen in the molten steel to a prescribed level. The steel is very clean because no deoxidizing elements that form solid oxides are added during the process.
Steel ingot
In addition, due to the different oxygen content in the molten steel before casting, the steel ingot is divided into three basic types: killed steel, boiling steel and semi-killed steel.
Calm steel
Also known as fully deoxidized steel, it is a steel in which the oxygen content in the molten steel is low enough to not react with carbon in the steel to form carbon monoxide bubbles. The molten steel before casting must be fully deoxidized. For example, deoxidation with silicon and aluminum, the silicon content of the steel is about 0.3%, and the aluminum content is (0.02-0.06%). The calmed steel ingots have shrinkage holes and must be cast with an ingot with a heat insulating cap. After the rolling, the ingot is cut, and the ingot yield is 85 to 89%. Steel ingots are required for steels with uniform composition and compact structure. The killed steel is made of a mold with a large upper and lower insulation cap. In recent years, heat insulation caps and heat insulation board insulation caps have been widely used to increase the blanking rate.
Boiling steel
The molten steel has a high oxygen content (0.02-0.04%), and a strong carbon-oxygen reaction occurs in the ingot mold to generate carbon monoxide bubbles, which is named after the molten steel boils in the mold. At the beginning of this steel solidification, bubbles form and float. The steel ingot skin is solidified into a relatively pure shell layer containing iron. When the surface layer reaches the required thickness, a cover plate is added on the top of the ingot to solidify the top to prevent the bubbles from continuing to escape; or a de-oxygenation of ferrosilicon, aluminum or the like may be added at the top for chemical capping; Capping. Another method is to add aluminum to the whole molten steel after the solidification of the molten steel into a surface layer. This steel ingot is called an outer boiling inner steel. Boiling steel generally adopts a bottle opening mold with a small upper and a large open type. The boiling steel ingot has a blanking rate of 90-92%, which is mainly used for low carbon steel.
Semi-killed steel
A steel grade between calm steel and boiling steel. This steel has less internal gas and is structurally close to killed steel. In the initial stage of semi-killed steel casting, no bubbles are generated. When the top is naturally solidified and capped (the bottle die can be used to promote the capping), due to the enrichment of carbon and oxygen in the molten steel and the temperature decrease, a small amount of carbon monoxide bubbles are generated on the top of the ingot, filling the whole. The solidification shrinkage space of molten steel. Therefore, the billet ratio of the steel ingot similar to that of the boiling steel can be obtained. Semi-killed steel is mainly used for medium-carbon and medium-quality structural steels. The molds used are generally open, small, and large.
Demoulding The cast ingot must be demolded after the interior is completely solidified. For alloy ingots with strong crack sensitivity, after demolding, they should be placed in a slow cooling pit in a hot state (>900 °C) for slow cooling, or sent to a soaking furnace in a rolling mill at a temperature not lower than 750 °C or Heating furnace.