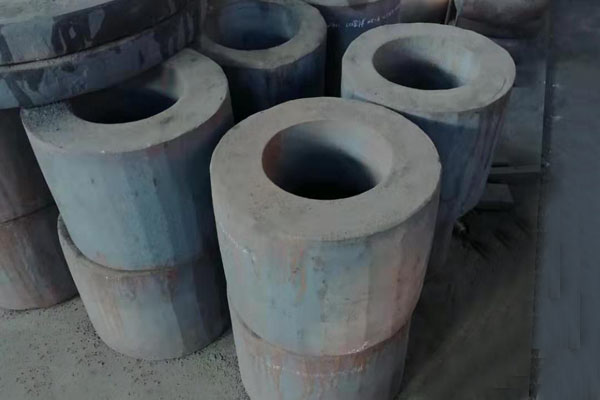
缩孔与疏松
该类孔隙性缺点,破坏金属陆续性,造成应力密集与裂纹源,属于不容许的缺点。
钢锭开坯时切除量不敷,残留缩孔及疏松,阐扬为锻件端头有管状孔穴大概紧张中间疏松。
对策是:
1)严酷控制浇注温度和速率,防止低温慢速注锭;
2)接纳发烧冒口或绝热冒口,改善补缩条件使缩孔上移至冒口区,防止缩孔深人到锭身处;
3)控制铸造时钢锭冒口切头率,充分切净缩松缺点。合理锻压变形,压实疏松缺点。
自由锻件批发哪家好,就找唐山盛通锻造有限公司。
Shrinkage and looseness
This type of porosity defect, which destroys the metal continuity, causes stress intensive and crack sources, and is an unacceptable disadvantage.
When the ingot is blanked, the amount of removal is not enough, and the residual shrinkage hole and looseness are expressed. The tubular hole at the end of the forging is probably tight and loose.
The countermeasures are:
1) Strictly control the pouring temperature and rate to prevent low temperature slow injection;
2) Accept the fever riser or the adiabatic riser, improve the feeding conditions, and move the shrinkage hole up to the riser area to prevent the shrinkage hole from reaching the ingot;
3) Control the rate of ingot cutting of steel ingots during casting, and fully cut the defects of shrinkage. Reasonable forging deformation, compaction and looseness.